The German sparkling wine market is highly competitive. To remain competitive, a cost-efficient production and bottling process is extremely important. A key technology is compressed air, which is required in all process steps – whether unpacking the sparkling wine bottles, filling and sealing, or labeling.
For this reason, the KESSLER sparkling wine cellar uses the SK 25 (9 kW) from FILCOM GmbH. KESSLER Sekt is one of the leading manufacturers in the premium sparkling wine market, accounting for approximately 15% of the market. The Esslingen site produces the Hochgewächs Brut, Jägergrün, and Réserve brands, among others. Two systems are in operation here, filling the sparkling wine into 0.75-liter, 0.375-liter, 0.2-liter piccolo, and 1.5-liter magnum bottles.

KESSLER SPARKLING WINE SINCE 1826.
KESSLER, Germany's oldest sparkling wine producer based in Esslingen am Neckar, has been committed to uncompromising quality for almost 200 years. Selected quality wines from Germany and Europe offer a unique taste experience. The "traditional method" is used for production, with an aging period of up to 60 months in historic cellars. KESSLER exports worldwide and sells almost two million bottles annually.
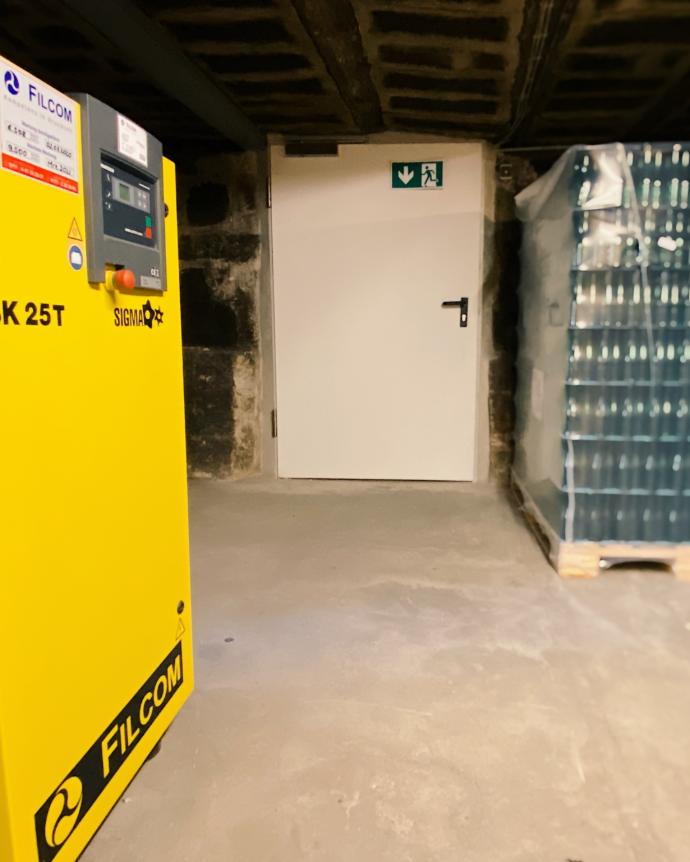
Challenge
Compressed air supports the machines during unpacking, cleaning, filling, capping, labeling, and repacking. This allows approximately 5,700 bottles to be handled per hour. This would be unthinkable without compressed air. A reliable compressed air supply is crucial to ensure smooth operations and consistent delivery.
Even when unpacking the champagne bottles, constant pressure is essential to suck the sterile bottles in using the Venturi effect and transport them from the pallet to the filling conveyor. Compressed air is also used in the subsequent filling process:
Activating the pneumatic valves during the various filling phases requires a pressure of 6 to 10 bar. Before the employees label and package the high-quality goods, the finishing touches take place: Final cleaning, in which compressed air removes tiny particles from the bottles, is mandatory. Then the product is ready for labeling. Targeted air pulses ensure the paper labels fit perfectly.
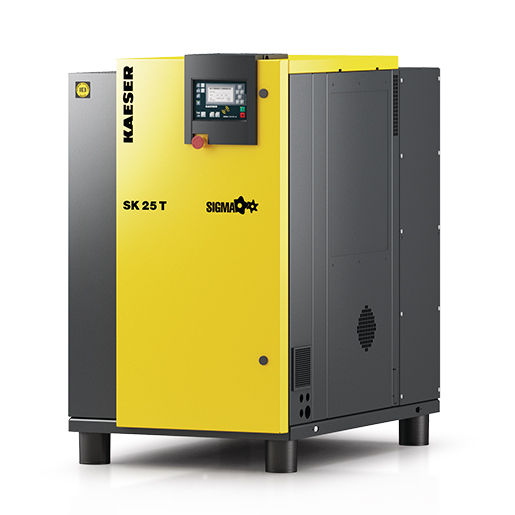
Solution statement
- At the KESSLER sparkling wine cellar in Esslingen, the KAESER SK 25 rotary screw compressor meets high demands for availability and efficiency. The KAESER rotary screw compressor, featuring the energy-saving "Sigma Profile," also features significantly increased air delivery and lower power consumption.
- An optimized compressor block minimizes internal pressure losses and reduces specific power requirements by up to 5 percent.
- The use of highly efficient Premium Efficiency motors (IE3) results in additional energy savings.
- The internal KAESER "Sigma Control" not only enables efficient control precisely tailored to the respective compressed air consumption, but also reliable operational monitoring.
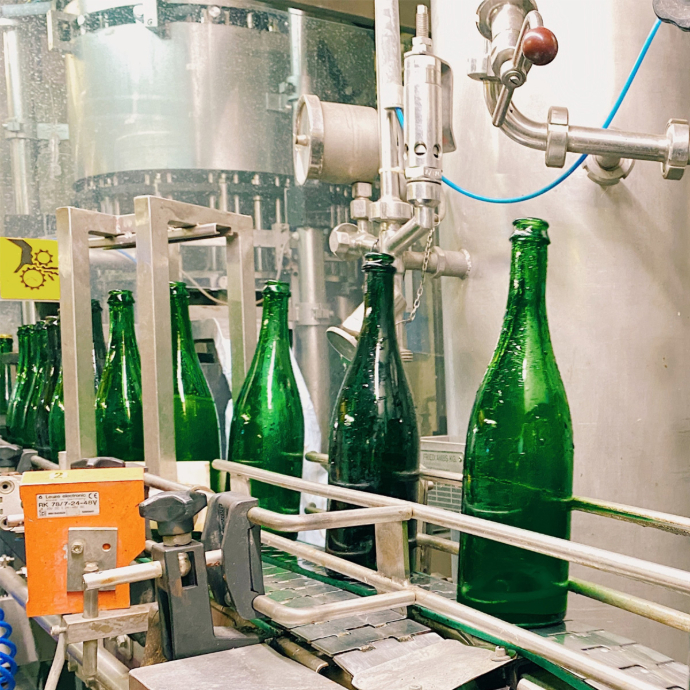
Customer benefit
- The KAESER fully meets customer expectations for high availability and efficiency. They not only produce more compressed air with less energy, but also leave nothing to be desired in terms of versatility, ease of operation and maintenance, and environmental friendliness.
- Thanks to the modular system concept, KESSLER Sekt uses the screw compressor with an integrated energy-saving refrigeration dryer. The integrated refrigeration dryer saves space. Thanks to a separate housing, the KAESER dryer is protected from the radiated heat of the KAESER compressor.