In the chemical and cosmetics industries, compressed air is far more than just an energy source – it is a crucial production factor. Whether for conveying raw materials, filling containers, or the sensitive cleaning of equipment: only perfectly treated compressed air guarantees process reliability, product purity, and legally compliant production. This current practical example shows how companies like SPEICK Naturkosmetik not only meet the highest quality standards with modern compressor technology and intelligent compressed air treatment, but also save energy.
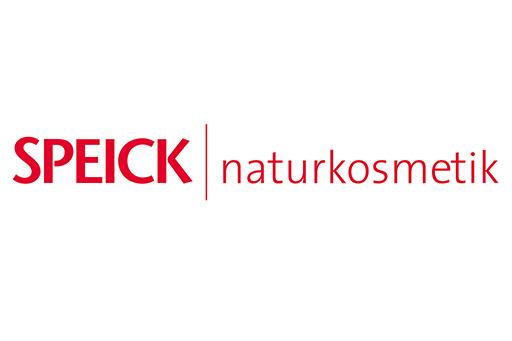
Speick Naturkosmetik GmbH & Co. KG
From a fine soap factory to a specialist in natural cosmetics: The success story of SPEICK Naturkosmetik began in 1928 with the introduction of the classic Speick soap, a trademark of the Stuttgart-based family business. The salmon-colored soap, with its characteristic scent and the extract of the Speick plant from the Carinthian Nock Mountains, was a groundbreaking innovation in body care at the time, as it not only cleansed but also cared for.
The Speick Original Soap is no longer the company's only flagship product. The product range currently includes approximately 140 items, including deodorants, shower gels, shampoos, face creams, and micellar water, all manufactured at the exclusive location in Leinfelden-Echterdingen. The company's popularity continues to grow as customers appreciate the naturalness of its products.
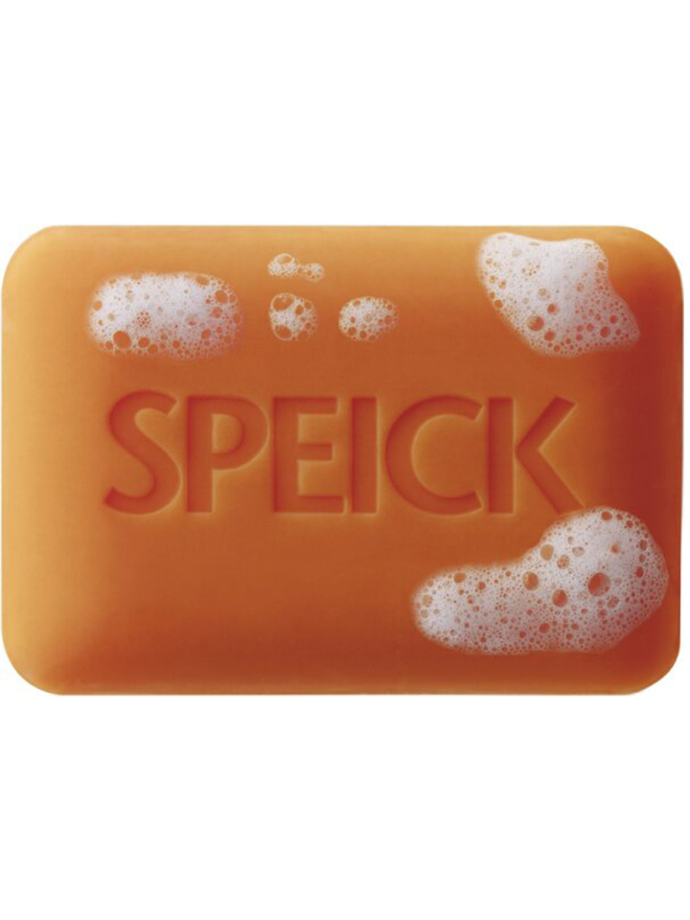
Challenge
Compressed air is crucial in the manufacturing processes of the cosmetics industry and is used in a wide variety of applications. It is generally used for cleaning equipment and containers, filling cosmetic products, transporting ingredients, operating packaging systems, and soap production, among other things. To ensure that the use of compressed air does not pose any risks to the manufacturing process and the quality of the final products, comprehensive treatment and continuous monitoring of the compressed air is required. Contaminants such as particles, moisture, germs, or oil aerosols must be effectively controlled, as they can enter the compressed air system in various ways.
In order to keep pace with production and manufacture as energy-efficiently as possible, SPEICK Naturkosmetik upgraded its compressed air supply with the help of FILCOM GmbH and technology from KAESER Kompressoren SE. For energy and operational reasons, the decision was made to replace the three existing screw compressors distributed throughout the production area, thus minimizing the time required for troubleshooting.

Solution statement
- SPEICK Naturkosmetik expects high availability and efficiency from its new compressor technology.
- The company quickly realized that these requirements could be met with two KAESER SK 25 series screw compressors.
- The SK models impress with their well-thought-out, user-friendly design.
- All maintenance points are easily accessible. When closed, the housing, with its sound-insulated paneling, ensures pleasant and quiet operation.
- In addition, three intake openings provide separate air supply for highly effective cooling of the system, the drive motor, and the control cabinet.
- Thanks to their vertical design, the SK compressors are real space savers.
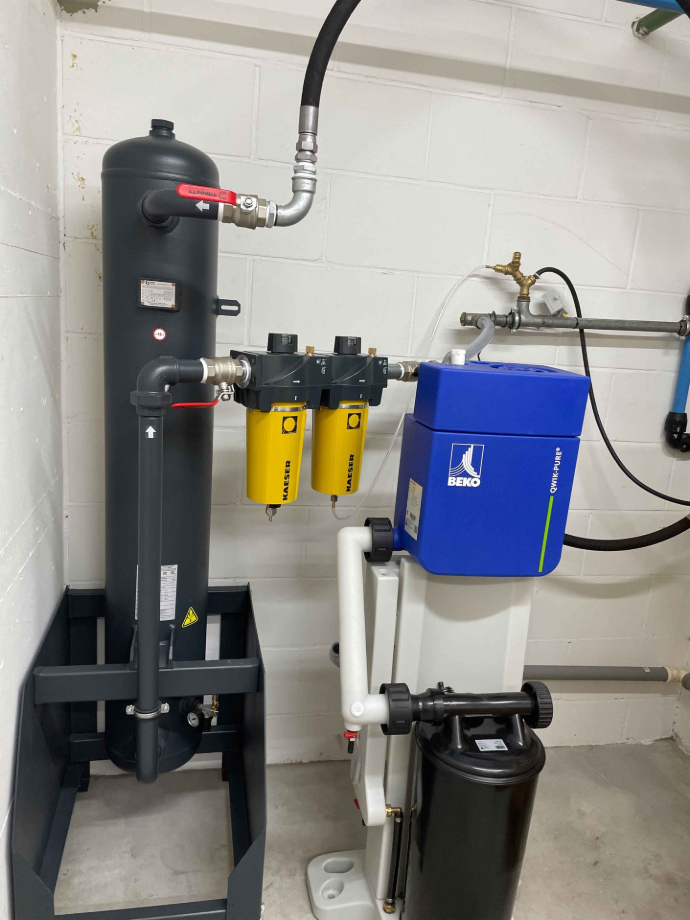
Customer benefit
- A KAESER SECOTEC TC 36 series refrigeration dryer is used to dry the compressed, moist air.
- Especially during partial load operation, the energy-saving control allows excess cooling capacity to be temporarily stored in the thermal storage tank and then accessed again for drying without consuming electricity.
- The fast-acting heat exchanger system ensures stable pressure dew points at all times.
- Significant quantities of oil-containing condensate are generated during compressed air generation. Oil-water separators adsorb the oil, ensuring dischargeable wastewater.
- SPEICK Naturkosmetik uses the QWIK-PURE 10 from BEKO Technologies for condensate treatment.
- By optimizing the compressed air, a valuable contribution was made to the long-term cost balance of the entire system.
- Two coalescing filters and a dust filter from KAESER Kompressoren ensure demand-based, reliable, and energy-efficient compressed air treatment.
- The system is configured to make troubleshooting in the event of a pressure drop very easy.
- The entire system can now be housed in a single utility room.
- In addition, compressed air optimization has significantly reduced costs.